Stud fasteners might not steal the spotlight, but they hold together the structures and machines we depend on daily. From cars to bridges, these components secure everything with strength and precision. So, what exactly are stud fasteners? They are threaded rods or pins—sometimes featuring a head on one end—that create robust, reliable joints across various applications. Unlike bolts or screws, stud fasteners offer unique flexibility and durability, making them essential in industries such as automotive, construction, and manufacturing.
In this article, we’ll explore stud fasteners in detail. First, we’ll define their purpose. Next, we’ll examine their types, uses, and benefits. After that, we’ll explain their installation and compare them to other fasteners. Whether you’re an engineer, a DIY enthusiast, or simply curious, this guide delivers clear, practical insights.
What Are Stud Fasteners?
Stud fasteners serve as mechanical devices that connect two or more parts securely. Unlike bolts with a head and partial threading, stud fasteners typically feature threading along their full length or at both ends. Engineers pair them with nuts or insert them into tapped holes to fasten materials, providing a versatile alternative to conventional options.
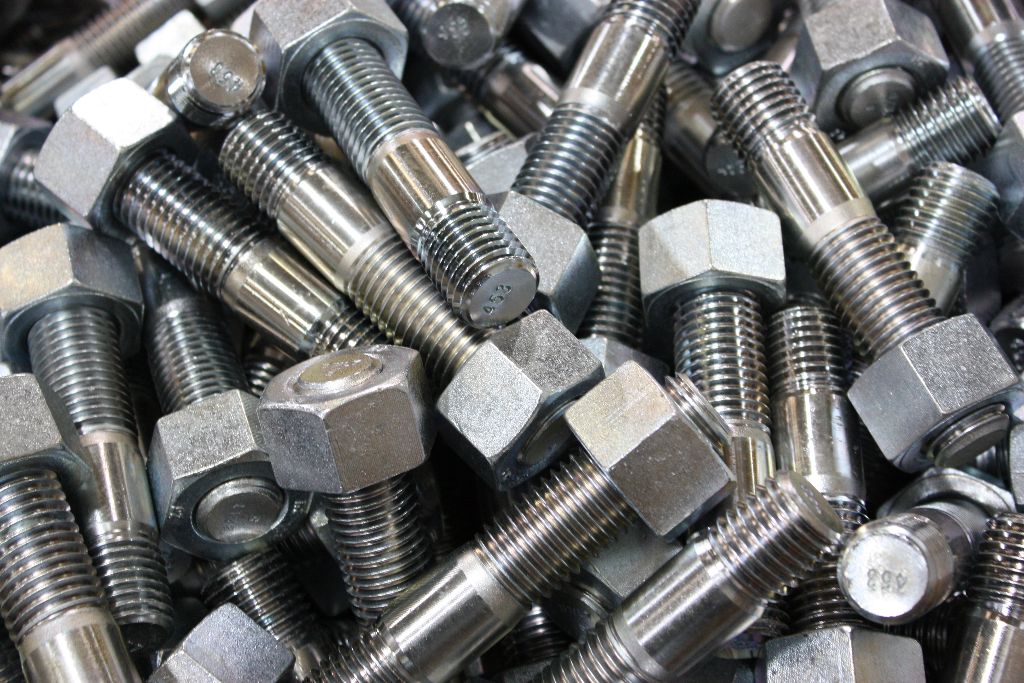
What makes stud fasteners unique is their adaptability. Installers can weld them to surfaces or press them into thin materials—options that bolts and screws don’t offer. This versatility suits applications needing strength, easy assembly, or frequent disassembly.
Manufacturers craft stud fasteners from various materials. They use steel for durability, stainless steel for corrosion resistance, and brass for specialized needs. They select the size, threading, and material based on the forces the fastener must withstand, such as tension in engines or shear stress in beams.
Types of Stud Fasteners
Stud fasteners come in multiple forms, each designed for specific purposes. Here’s a breakdown of the main types:
Threaded Studs
First, threaded studs are cylindrical rods with threads along their entire length or at both ends. Installers secure them with nuts, creating strong yet removable joints.
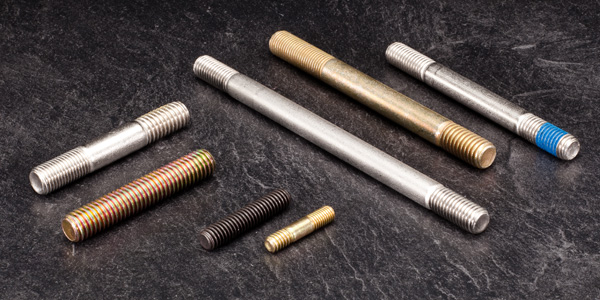
- Design: Fully or double-end threaded rods, no fixed head.
- Purpose: Deliver adjustable, high-strength connections.
- Applications: Pipe flanges, engine cylinder heads, and steel frameworks.
- Example: Mechanics use threaded studs in car engines to hold cylinder heads, allowing easy removal for repairs.
Weld Studs
Next, weld studs attach permanently to surfaces through welding. Industries choose them when drilling through materials isn’t feasible.
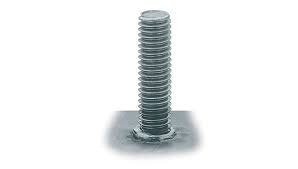
- Design: Often include a small head or no head, with one end suited for welding.
- Purpose: Provide a fixed, durable fastening point.
- Applications: Automotive panels, electrical enclosures, and bridge construction.
- Example: Workers weld studs to car chassis in manufacturing, speeding up assembly without extra holes.
Press-In Studs
Then, press-in studs fit into pre-drilled holes, where installers press them into place. Their serrated sections grip the material, making them ideal for thin surfaces.
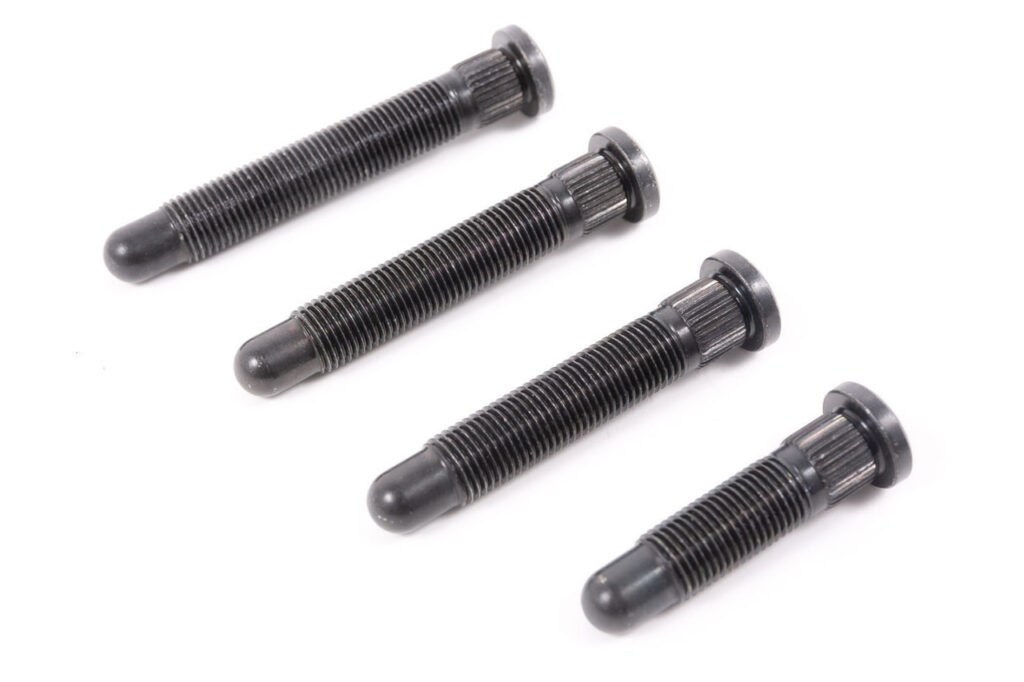
- Design: Feature textured sections for grip, often with a small head.
- Purpose: Create threaded points in lightweight components.
- Applications: Sheet metal in panels, automotive trim, and appliances.
- Example: Technicians use press-in studs in computer cases to mount circuit boards efficiently.
Clinch Studs
Finally, clinch studs resemble press-in studs but lock into place by deforming the surrounding material. Manufacturers rely on them for permanent sheet metal fastening.
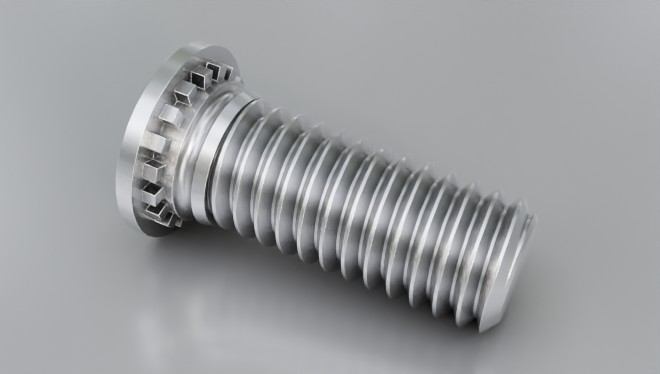
- Design: Include a flange or head that sits flush after installation.
- Purpose: Offer a strong, non-removable threaded point.
- Applications: HVAC ducts, metal furniture, and signage.
- Example: Builders use clinch studs in air conditioning units to secure panels tightly.
Each type meets distinct needs. Therefore, selecting the right stud fastener depends on your project’s material, stress, and assembly demands.
Applications of Stud Fasteners
Stud fasteners support countless industries by solving practical fastening challenges. Here’s how different sectors use them:
- Automotive: The automotive industry uses weld studs to attach body panels and brackets. Additionally, threaded studs secure engine parts like cylinder heads and exhaust systems, offering strength for fast production.
- Construction: Builders install threaded studs to connect plumbing pipe flanges. Moreover, they weld studs to steel beams in skyscrapers and bridges, ensuring long-lasting durability.
- Manufacturing: Manufacturers press or clinch studs into sheet metal for products like enclosures and appliances. This streamlines assembly and cuts costs.
- Aerospace: Engineers use stud fasteners in aircraft to secure wings, fuselages, and landing gear. Their strength under stress and vibration ensures safety.
- Marine: The marine sector employs stainless steel studs to resist corrosion in boats and offshore platforms, maintaining reliable joints in harsh conditions.
From everyday items to advanced technology, stud fasteners provide strength and adaptability wherever needed.
Advantages of Stud Fasteners
Why opt for stud fasteners? Their benefits set them apart from other fastening solutions:
- Ease of Installation: For example, weld studs skip drilling and tapping, while threaded studs simplify complex assemblies. This reduces time and labor costs.
- Strength and Durability: Engineers design stud fasteners to handle high tension and shear, making them perfect for engines and steel structures.
- Versatility: With options for thin sheets or thick plates, stud fasteners suit a wide range of materials and setups.
- Reusability: Mechanics can remove and reinstall threaded studs without damaging materials, ideal for maintenance-heavy equipment.
- Space Efficiency: In tight spaces, stud fasteners deliver secure joints without the bulk of bolts or extra clearance needs.
Compared to bolts or screws, stud fasteners excel in applications needing frequent access or permanent bonds. Thus, they balance strength and practicality effectively.
Installation of Stud Fasteners
Installing stud fasteners varies by type, but each method is manageable with proper tools. Here’s how to install them:
Threaded Studs
- Method: Screw the stud into a tapped hole or secure it with nuts on both ends.
- Tools: Use a wrench or socket set.
- Tips: Apply even torque to protect threads. Additionally, use thread-locking compounds in vibrating settings.
Weld Studs
- Method: Weld the stud to a surface with arc or capacitor discharge welding.
- Tools: Employ a stud welding gun.
- Tips: Clean the surface for a strong weld. Then, test the bond for reliability.
Press-In Studs
- Method: Insert into a pre-drilled hole and press into place, letting the serrated section grip the material.
- Tools: Use a manual or hydraulic press.
- Tips: Match the hole size to the stud to avoid weak holds or cracks.
Clinch Studs
- Method: Place into a hole and press to deform the material around the stud, locking it in.
- Tools: Use a clinching press.
- Tips: Check material thickness for proper deformation and a flush finish.
Proper installation maximizes strength. Therefore, follow manufacturer guidelines and use quality tools to prevent misalignment or damage.
Comparison with Other Fasteners
Stud fasteners differ from bolts and screws, each offering unique strengths. Here’s how they stack up:
Stud Fasteners vs Bolts
- Design: Studs lack heads and feature full or double-end threading, while bolts have heads and partial threading.
- Strength: Studs distribute stress more evenly, especially with double nuts.
- Use Cases: Studs suit removable joints (e.g., engine repairs), whereas bolts work for one-sided fastening.
- Installation: Studs need nuts or tapped holes, but bolts require only a wrench.
Stud Fasteners vs Screws
- Design: Studs lack self-tapping ends, while screws cut their own threads.
- Strength: Studs with nuts often bear higher loads than screws alone.
- Use Cases: Studs pair with pre-tapped holes or nuts, whereas screws fasten directly into materials.
- Installation: Studs use extra components (nuts), but screws stand alone.
In short, stud fasteners shine in complex, strong, or removable joints, while bolts and screws fit simpler needs.
Conclusion
Stud fasteners do more than connect parts—they underpin the reliability of our world. From threaded studs in engines to weld studs in skyscrapers, their variety, applications, and advantages make them vital across industries. They deliver unmatched strength, versatility, and ease, outpacing other fasteners in many scenarios.
For companies making these components, precision matters. Xiluo Mold, with over 23 years of expertise in high-precision mold manufacturing, ensures stud fasteners meet top standards—offering quality you can rely on.
Next time you tackle a project, consider stud fasteners for their durability and flexibility. They could be the ideal solution.