Threading powers the world of fasteners, securing everything from your car’s engine to the beams of a skyscraper. Without it, bolts, screws, and nuts wouldn’t hold anything together. But what does all that jargon—like “pitch,” “crest,” or “major diameter”—actually mean? Understanding threading terminology unlocks the secrets of how fasteners work, helping engineers design better machines, manufacturers choose the right components, and DIYers tackle projects with confidence.
In this guide, we’ll dive into the essential terms that define threading. First, we’ll explain what threading is and why it matters. Next, we’ll break down key terms with clear definitions and examples. Then, we’ll compare metric and imperial threading systems. Finally, we’ll explore how these terms apply in the real world. Whether you’re a pro or just curious, this article simplifies the spiral world of threads.
What Is Threading?
Threading creates the magic behind fasteners. Engineers carve spiral grooves—called threads—onto bolts, screws, or nuts, allowing them to rotate into place and lock materials together. These helical ridges provide grip, strength, and adjustability, making threaded fasteners indispensable in construction, manufacturing, and beyond.
Why does threading matter? For one, it ensures a secure, reusable connection. Unlike nails, threaded fasteners let you assemble and disassemble parts without damage. Plus, they distribute stress evenly, preventing joints from failing under pressure. From tiny screws in your phone to massive bolts in bridges, threading makes precision possible.
Manufacturers rely on threading to meet exact standards. Every term we’ll cover—pitch, diameter, and more—shapes how a fastener performs. So, let’s explore these concepts and see how they come to life.
Key Threading Terms
Threading terminology can feel like a maze, but each term has a clear purpose. Here’s a detailed look at the essentials:
Pitch
Pitch measures the distance between adjacent threads. Imagine looking at a screw sideways—pitch is the space from one thread’s peak to the next.
- How It Works: A finer pitch (smaller distance) means more threads per inch, offering better grip for high-pressure applications.
- Example: In an automotive engine, a fine pitch seals components tightly against leaks.
Crest
The crest crowns the thread. It’s the highest point, forming the outer edge you see when inspecting a bolt.
- How It Works: The crest defines the thread’s outer boundary, influencing how it mates with a nut or tapped hole.
- Example: A sharp crest on a bolt ensures a snug fit in heavy machinery.
Root
The root sits at the thread’s base, nestled between the ridges. It’s the lowest point, opposite the crest.
- How It Works: A deeper root strengthens the thread by providing more material to resist breaking.
- Example: In construction bolts, a sturdy root handles the weight of steel beams.
Thread Angle
Thread angle describes the slope between a thread’s sides, or flanks. Most threads use a 60-degree angle, though some vary.
- How It Works: A steeper angle increases strength but complicates manufacturing; a flatter angle eases production but may weaken grip.
- Example: Aerospace bolts often use a precise 60-degree angle for durability under extreme forces.
Major Diameter
Major diameter spans the widest part of the thread, from crest to crest across the fastener.
- How It Works: It determines the fastener’s overall size and load capacity—larger diameters handle more stress.
- Example: A 1/2-inch major diameter bolt supports heavy structural joints.
Minor Diameter
Minor diameter measures the narrowest part, from root to root. It’s the core of the fastener.
- How It Works: A smaller minor diameter leaves more thread depth, boosting strength but reducing core material.
- Example: Fine-thread screws in electronics use a small minor diameter for precision.
Lead
Lead tracks how far a fastener advances with one full turn. For single-threaded fasteners, lead equals pitch; for multi-threaded ones, it’s pitch times the number of starts.
- How It Works: A larger lead speeds up installation but may sacrifice holding power.
- Example: A double-threaded bolt in furniture assembly moves twice as fast per turn.
Thread Series
Thread series standardizes thread sizes. Common ones include UNC (Unified National Coarse), UNF (Unified National Fine), and ISO metric.
- How It Works: Each series sets pitch and diameter rules for consistency across industries.
- Example: UNC bolts suit general construction, while UNF bolts excel in precision machinery.
Thread Fit
Thread fit defines how tightly a bolt and nut mesh. Classes like 1, 2, and 3 (for imperial) or 6g, 6h (for metric) range from loose to snug.
- How It Works: A tighter fit (e.g., Class 3) resists vibration but requires precision; a looser fit (e.g., Class 1) eases assembly.
- Example: Class 3 fits secure aircraft engines, where every thread counts.
These terms shape every fastener’s design and performance. Next, we’ll compare how they differ between metric and imperial systems.
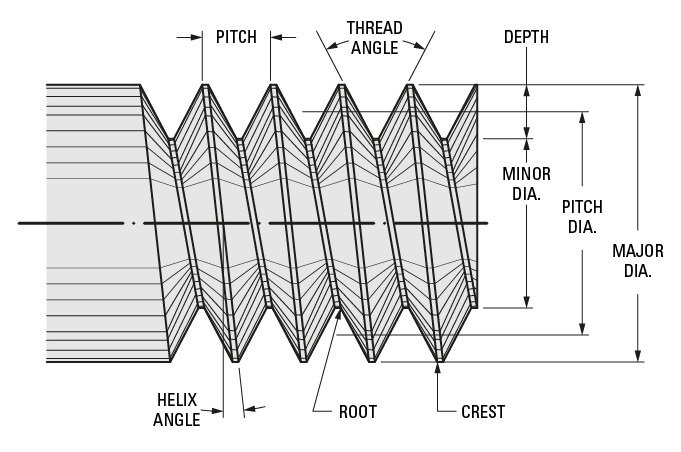
Metric vs. Imperial Threading Terms
Threading splits into two worlds: metric and imperial. Each uses unique terms and measurements, so let’s break them down.
Metric Threads
Metric threads measure pitch in millimeters. A label like “M6-1.0” means a 6mm major diameter with a 1mm pitch.
- Key Features: Pitch defines spacing (e.g., 1.0mm between threads). ISO standards ensure global consistency.
- Uses: Dominant in Europe, Asia, and most modern manufacturing—think cars and electronics.
- Example: An M8-1.25 bolt fastens automotive parts with precision.
Imperial Threads
Imperial threads count threads per inch (TPI). A label like “1/4-20 UNC” means a 1/4-inch major diameter with 20 threads per inch.
- Key Features: TPI replaces pitch (e.g., higher TPI = finer threads). Unified National standards (UNC, UNF) rule in the U.S.
- Uses: Common in American construction, machinery, and legacy equipment.
- Example: A 3/8-16 UNC bolt secures steel frames in U.S. buildings.
Comparison
- Measurement: Metric uses millimeters for pitch; imperial uses TPI.
- Naming: Metric starts with “M” (e.g., M10); imperial uses fractions or gauges (e.g., 1/2-13).
- Application: Metric suits global industries; imperial thrives in U.S.-centric projects.
For example, a mechanic in Germany might use an M10 bolt, while one in the U.S. grabs a 3/8-16. Understanding both systems helps you navigate any job.
Related articles: Screw Sizes Explained: Your Guide to Standard and Metric Sizes
Real-World Applications of Threading Terms
Threading terminology isn’t just theory—it drives real-world decisions. Here’s how these terms play out:
Manufacturing
Manufacturers use terms like pitch and thread series to craft fasteners. A fine pitch (e.g., UNF or M6-0.75) seals high-pressure engine parts, while a coarse pitch (e.g., UNC) speeds up assembly in mass production.
- Example: A factory producing car bolts chooses a tight thread fit (Class 3) to prevent loosening under vibration.
Fastener Selection
Choosing the right thread depends on load, material, and environment. A larger major diameter handles heavy loads in construction, while stainless steel threads resist rust in marine settings.
- Example: A bridge builder selects a 1-inch major diameter bolt with a coarse pitch for quick, strong connections.
Everyday Use
Even DIYers benefit from threading knowledge. A finer thread grips hardwood better, while a looser fit eases furniture assembly.
- Example: A homeowner uses a 1/4-20 bolt for a shelf, balancing strength and ease of installation.
These terms guide everything from design to installation, ensuring fasteners perform as intended.
Conclusion
Threading terminology unlocks the science of fasteners. From pitch and crest to thread fit and lead, each term defines how bolts, screws, and nuts hold our world together. Whether you’re comparing metric and imperial systems or picking the right thread for a job, understanding these concepts ensures precision and reliability.
For manufacturers, these terms are the blueprint for quality. Companies like Xiluo Mold, with over 23 years of expertise in high-precision fastener mold manufacturing, rely on this knowledge to create molds that produce top-tier threaded components. Next time you twist a bolt into place, you’ll know exactly what makes it work—and why it matters.