1. Introduction
In the world of fastener manufacturing, flat thread rolling dies are indispensable tools that shape the threads of screws, bolts, and other components with precision and efficiency. These dies play a critical role in ensuring the quality and consistency of threaded fasteners, which are vital across industries like automotive, aerospace, and construction. As a seasoned manufacturer with over two decades of experience in fastener mold production, we understand the nuances of designing flat thread rolling dies that meet rigorous industry demands. This guide will walk you through the fundamental principles, key design considerations, common challenges, and emerging trends in flat thread rolling die design, offering practical insights to help you optimize your manufacturing process.
2. Understanding Flat Thread Rolling Dies: The Basics
A flat thread rolling die is a specialized mold used in the cold-forming process to create threads on cylindrical workpieces. Unlike cutting methods, thread rolling uses two flat dies—one stationary and one moving—each engraved with grooves that mirror the desired thread profile. When a workpiece is placed between the dies and pressure is applied, it rolls and deforms plastically, forming threads without removing material. This process offers several advantages: higher production speeds, improved thread strength due to work hardening, and exceptional precision. Understanding this mechanism is the foundation of effective die design, as every element—from material to geometry—must align with the thread-forming process.
3. Key Elements of Flat Thread Rolling Die Design
Designing a flat thread rolling die requires careful attention to multiple factors that influence performance, durability, and output quality. Below, we explore the three most critical elements.
3.1 Material Selection
The choice of material is the cornerstone of a high-performing flat thread rolling die. The ideal material must withstand high pressure, resist wear, and maintain structural integrity over thousands of cycles. High-speed steels (e.g., M2, M42) and premium tool steels (e.g., DC53, D55) are popular choices due to their excellent hardness and toughness. For demanding applications, carbide inserts may be integrated to enhance durability. At our company, we source top-grade imported steels, ensuring our dies deliver consistent performance even under intense workloads.
3.2 Dimensions and Tolerances
Precision in dimensions and tolerances is non-negotiable in flat thread rolling die design. The die’s groove profile must match the workpiece’s thread specifications—pitch, depth, and angle—down to micrometer-level accuracy. Even slight deviations can lead to defective threads or premature die wear. For example, a standard M8 thread requires a pitch of 1.25 mm, and the die’s tolerances must stay within ±0.005 mm to ensure uniformity. Our advanced machining capabilities and rigorous quality checks allow us to achieve such precision, tailoring each die to the client’s exact requirements.
3.3 Surface Treatment
Surface treatment enhances a die’s resistance to wear, friction, and fatigue, directly impacting its lifespan and performance. Common treatments include heat treatment for increased hardness, nitriding for improved surface durability, and titanium nitride (TiN) coating for reduced friction. Polishing the die surface also minimizes material buildup and ensures smoother thread formation. We offer a range of customizable surface treatments, adapting to specific operating conditions like high-speed production or corrosive environments.
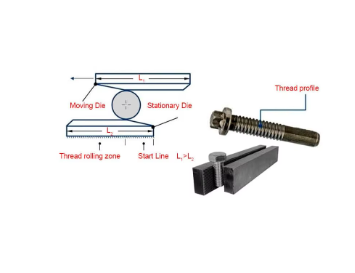
4. Common Design Challenges and Solutions
Even with a solid design foundation, flat thread rolling dies face challenges that can compromise their effectiveness. Here’s how to address two prevalent issues.
4.1 Wear and Lifespan
Wear is an inevitable challenge in thread rolling due to the constant friction and pressure between the die and workpiece. Factors like poor material choice, inadequate lubrication, or suboptimal groove design accelerate wear, reducing die lifespan. To combat this, designers can opt for wear-resistant materials, apply advanced coatings (e.g., nano-coatings), and optimize groove angles to distribute stress evenly. Regular maintenance, such as regrinding worn surfaces, also extends usability. Our experience shows that a well-designed die, paired with proper care, can achieve lifespans exceeding 500,000 cycles.
4.2 Precision and Consistency
Achieving consistent thread accuracy across thousands of parts is a core objective of die design. Misalignment, thermal expansion, or manufacturing defects can introduce variations that affect thread quality. Solutions include using high-precision CNC machining for die production, incorporating cooling systems to manage heat, and implementing strict quality control with tools like profile projectors and coordinate measuring machines (CMM). Our in-house testing ensures every die meets international standards, such as ISO or DIN, delivering reliable results for our clients.
5. Innovative Trends in Flat Thread Rolling Die Design
The fastener industry is evolving, and flat thread rolling die design is keeping pace with cutting-edge advancements. One trend is the adoption of advanced materials, such as powder metallurgy steels, which offer superior toughness and wear resistance. Another is the use of nanotechnology-based coatings, like diamond-like carbon (DLC), to further reduce friction and extend die life. Smart manufacturing is also gaining traction, with sensor-equipped dies providing real-time data on wear and performance, enabling predictive maintenance. Additionally, 3D simulation software now allows designers to test die performance virtually before production, minimizing errors and costs. Staying ahead of these trends ensures manufacturers remain competitive in a demanding market.
6. Conclusion
Designing flat thread rolling dies is a complex but rewarding endeavor that blends engineering precision with practical problem-solving. From selecting durable materials to mastering tolerances and embracing innovation, each step contributes to creating dies that enhance fastener quality and production efficiency. As a professional manufacturer with 23 years of expertise, Dongguan Xiluo Mold Technology Co., Ltd. is committed to delivering high-quality flat thread rolling dies tailored to our clients’ needs. Our focus on precision, durability, and customer-centric solutions has made us a trusted partner in the fastener industry. Whether you’re refining your design process or seeking reliable molds, this guide offers a starting point to elevate your manufacturing capabilities.