Cold forming dies are the workhorses of the fastener and metal parts industry, enduring immense forces to shape metal with precision. However, their demanding operational environment makes them susceptible to various modes of failure that can halt production. Understanding the common failures of cold forming dies – such as wear, cracking, chipping, and galling – is crucial, as implementing specific preventative measures in material selection, design, heat treatment, and maintenance can significantly extend tool life and minimize costly downtime. Addressing these issues proactively ensures consistent part quality and optimizes manufacturing efficiency.
This article will delve into the most frequent types of cold forming die failures. We will examine their root causes and, most importantly, provide actionable strategies for prevention. By understanding and mitigating these common problems, manufacturers can significantly enhance die longevity and production reliability.
Table of Contents:
- What Are the Most Common Types of Cold Forming Die Failures?
- What Causes Wear in Cold Forming Dies and How Can It Be Prevented?
- How Do Cracking and Chipping Occur in Dies, and What Are the Solutions?
- What Is Galling (Adhesion) in Dies, and How Can It Be Minimized?
- How Do Material Selection and Heat Treatment Impact Die Failure?
- What Role Do Design and Maintenance Play in Preventing Die Failures?
What Are the Most Common Types of Cold Forming Die Failures?
The most common types of cold forming die failures include abrasive wear, adhesive wear (galling), chipping, and cracking, each stemming from distinct stress mechanisms and material interactions during the forming process. These failures significantly reduce die lifespan, compromise part quality, and lead to costly production interruptions. Understanding each failure mode is the first step toward effective prevention strategies.
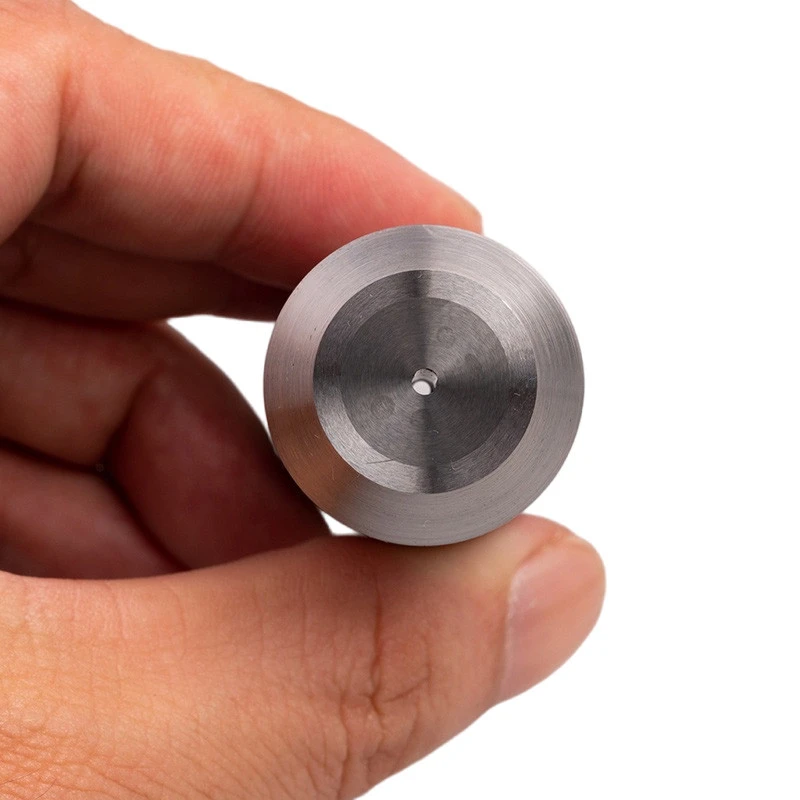
Cold forming dies operate under extreme conditions. High compressive forces, friction, and repetitive impacts constantly stress the die material. This harsh environment makes dies vulnerable to various forms of degradation. Each type of failure manifests differently and requires specific preventative measures. Recognizing the signs of each type of failure is crucial for timely intervention and avoiding more extensive damage.
What Causes Wear in Cold Forming Dies and How Can It Be Prevented?
Wear in cold forming dies is primarily caused by abrasive friction from material flow and adhesive transfer (galling), which gradually erodes the die’s precise geometry. Prevention strategies focus on enhancing the die surface through superior material hardness, applying advanced low-friction coatings, and ensuring proper lubrication during the cold forming process. Minimizing direct metal-on-metal contact is key.
Causes of Wear:
- Abrasive Wear: Hard particles (e.g., carbides in the workpiece, scale, debris) scratch and cut the die surface. This leads to gradual material removal.
- Adhesive Wear (Galling/Seizing): Workpiece material sticks to the die surface. This occurs due to high pressure and friction. As the material continues to flow, fragments pull away from both the die and the workpiece. This results in rough surfaces and material transfer.
- Fatigue Wear: Repeated cyclic loading can lead to surface fatigue. This results in pitting or spalling, especially in areas of high stress concentration.
Prevention Strategies for Wear:
- Optimal Die Material Selection: Choose tool steels (e.g., high-speed steel, powder metallurgical steel) or carbide inserts with high inherent hardness and wear resistance.
- Advanced Surface Coatings: Apply coatings like TiN, TiCN, AlTiN, CrN, or DLC. These provide a much harder, lower-friction surface. They act as a barrier against abrasive and adhesive wear.
- Effective Lubrication: Use appropriate cold forming lubricants. These create a separating film between the die and workpiece. This significantly reduces friction and prevents galling.
- Proper Surface Finish: Ensure the die surface is highly polished. A smooth finish reduces friction and minimizes sites for material adhesion.
- Workpiece Material Quality: Control the cleanliness and surface finish of the raw material. This reduces abrasive particles entering the die.
How Do Cracking and Chipping Occur in Dies, and What Are the Solutions?
Cracking and chipping in cold forming dies primarily result from excessive brittleness, improper stress distribution, or thermal shock, causing sudden fracture or localized material loss, particularly at sharp corners or highly stressed areas. Solutions involve precise heat treatment to balance hardness and toughness, optimized die design to reduce stress concentrations, and careful handling during operation and maintenance. These failures are often catastrophic.
Causes of Cracking and Chipping:
- Insufficient Toughness (Brittleness): The die material is too hard or improperly tempered. It cannot absorb impact energy without fracturing.
- Stress Concentrations: Sharp corners, abrupt changes in cross-section, or design flaws can create localized stress points. These points exceed the material’s strength limits.
- Quench Cracks: Improper cooling rates during heat treatment can induce severe internal stresses. This leads to immediate cracking.
- Fatigue Cracks: Repetitive loading cycles can initiate microscopic cracks. These propagate over time, leading to eventual fracture.
- Thermal Shock: Rapid temperature changes (e.g., sudden cooling if a die gets hot during operation) can induce stresses that cause cracking.
- Impact Overload: Exceeding the die’s design load due to machine misalignment or incorrect setup can cause sudden fracture.
Prevention Strategies for Cracking and Chipping:
- Optimized Heat Treatment: Precisely control hardening and tempering processes. This achieves an ideal balance between hardness (for wear resistance) and toughness (for impact absorption). Cryogenic treatment can also improve toughness.
- Robust Die Design: Design dies with generous radii and smooth transitions. This minimizes stress concentrations. Ensure adequate support for critical areas.
- Proper Die Material Selection: Choose tool steels known for good toughness at the required hardness level (e.g., certain PM steels).
- Correct Alignment & Machine Setup: Ensure the die and punch are perfectly aligned in the cold heading machine. This distributes forces evenly.
- Controlled Operating Parameters: Avoid excessive forming forces or rapid impacts that exceed the die’s design limits.
- Stress Relieving: Consider periodic stress-relieving heat treatments for highly stressed dies. This reduces built-up internal stresses.
What Is Galling (Adhesion) in Dies, and How Can It Be Minimised?
Galling in dies, also known as adhesive wear, occurs when workpiece material adheres to the die surface due to high pressure and friction, leading to material transfer, surface roughening, and eventual tool degradation. This phenomenon is particularly common with ductile materials like stainless steel and aluminum. Minimization strategies focus on reducing friction, preventing material bonding, and using surfaces that are resistant to adhesion.
Causes of Galling:
- High Pressure and Friction: The intense contact pressure between the die and workpiece, combined with relative motion, creates conditions for cold welding.
- Material Compatibility: Certain material combinations (e.g., stainless steel on tool steel) have a strong tendency to adhere to each other.
- Insufficient Lubrication: An inadequate or broken lubricating film allows direct metal-to-metal contact, promoting adhesion.
- Rough Die Surface: Irregularities on the die surface can act as anchor points for workpiece material.
- High Ductility of Workpiece: Softer, more ductile materials are more prone to deformation and adhesion.
Minimization Strategies for Galling:
- Anti-Galling Coatings: Apply specialized coatings like CrN, DLC, or specific TiCN variants. These coatings have low coefficients of friction and poor adhesion properties with workpiece materials.
- Effective Lubrication System: Use high-performance cold forming lubricants specifically designed for anti-galling. Ensure proper application and replenishment throughout the process.
- Die Material Selection: Consider die materials with an inherently lower tendency to gall with the workpiece, or use carbide inserts where galling is severe.
- Optimal Surface Finish: Polish the die surface to a very high degree (mirror-like finish). A smoother surface reduces adhesion points.
- Die Design Optimization: Design die geometry (e.g., radii, lead-in angles) to promote smooth material flow. This minimizes areas where material can accumulate or become trapped.
- Workpiece Surface Preparation: Sometimes, pre-coating or special surface treatments on the workpiece itself can help prevent galling.
How Do Material Selection and Heat Treatment Impact Die Failure?
Material selection and heat treatment are foundational in preventing cold forming die failures, as they determine the die’s inherent mechanical properties like hardness, toughness, wear resistance, and dimensional stability. The chosen tool steel must possess the correct chemical composition, and heat treatment must precisely unlock and optimize these properties to withstand the severe stresses of cold forming operations. Compromises in either area directly lead to premature failure.
Material Selection Impact:
- Base Properties: The chemical composition of the tool steel (e.g., carbon content, alloying elements like chromium, molybdenum, vanadium) dictates its potential for hardness, wear resistance, and toughness after heat treatment.
- Trade-offs: Selecting a material often involves a trade-off. For example, higher hardness usually means lower toughness. Designers must balance these based on the specific application’s demands (e.g., impact vs. abrasion).
- Inclusions and Homogeneity: High-quality, clean tool steels with uniform microstructure are less prone to failure. Impurities or segregation can act as stress concentrators.
- Examples:
- High-Speed Steels (HSS): Good balance of hardness and toughness; common for general-purpose dies.
- Powder Metallurgical (PM) Steels: Offer superior wear resistance and toughness due to finer grain structure and more uniform carbide distribution; ideal for demanding applications.
- Tungsten Carbide: Extremely hard and wear-resistant; used for inserts in high-volume or highly abrasive applications.
Heat Treatment Impact:
- Hardness & Brittleness Control: Precise heat treatment (austenitizing, quenching, tempering) achieves the targeted hardness while mitigating brittleness. Too hard, it cracks; too soft, it wears.
- Stress Relief: Proper tempering and multi-tempering cycles relieve internal stresses induced during quenching. This prevents distortion and cracking.
- Microstructure Optimization: Heat treatment controls the size and distribution of carbides and other phases. This directly influences wear resistance and toughness.
- Dimensional Stability: Controlled heat treatment minimizes changes in die dimensions, crucial for maintaining tight tolerances in formed parts.
- Prevention of Retained Austenite: For certain steels, cryogenic treatment can convert retained austenite (a softer phase) into harder martensite, improving performance and stability.
Ultimately, the synergy between a well-chosen material and expertly executed heat treatment is paramount for die longevity.
What Role Do Design and Maintenance Play in Preventing Die Failures?
Die design and ongoing maintenance play indispensable roles in preventing cold forming die failures by optimizing stress distribution, ensuring proper material flow, and preserving the die’s integrity throughout its operational life. A robust design minimizes inherent weaknesses, while meticulous maintenance detects and addresses issues before they escalate into catastrophic failures, collectively ensuring maximum die lifespan and consistent production. These factors are within the manufacturer’s direct control.
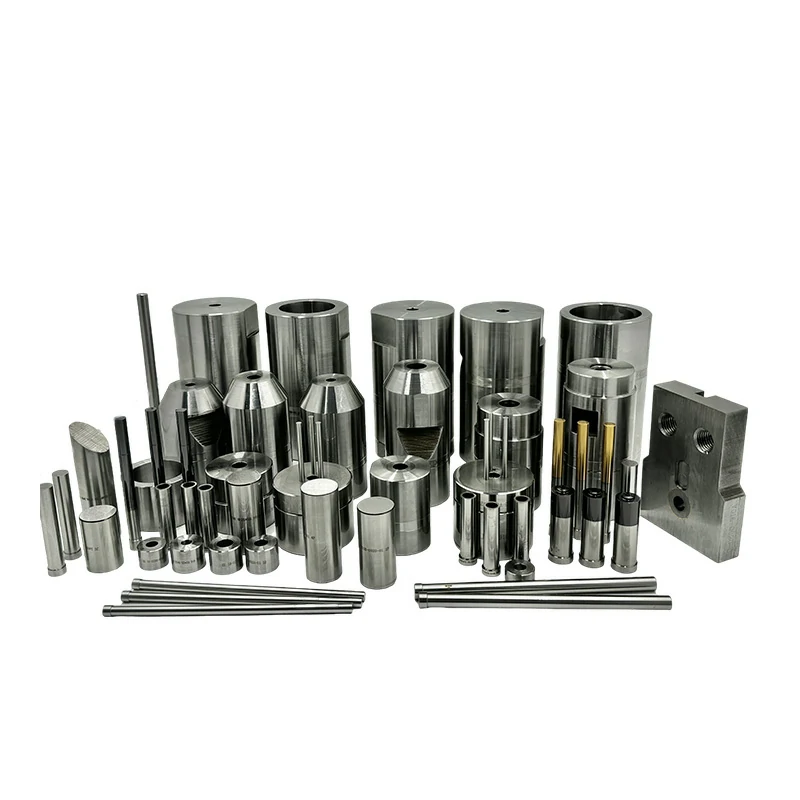
Role of Die Design:
- Stress Mitigation:
- Radii & Fillets: Generous radii at corners and transitions reduce stress concentration points where cracks typically initiate.
- Uniform Cross-Sections: Avoiding abrupt changes in section thickness can help ensure uniform cooling during heat treatment and minimize stress gradients.
- Support & Confinement: Designing dies with adequate support and backing rings (for carbide inserts) helps manage compressive stresses.
- Optimized Material Flow:
- Lead-in Angles & Tapers: Proper design of the die entry and forming angles guides the workpiece material smoothly into the cavity. This prevents folds, laps, and excessive friction.
- Vent Holes: Strategic placement of vent holes allows air to escape during forming, preventing pressure buildup and ensuring full form filling.
- Surface Finish Considerations: Designers specify the required surface finish for different areas of the die. A highly polished finish reduces friction and galling.
- Modularity: Designing dies with interchangeable inserts allows replacement of worn components without replacing the entire die body, reducing cost and waste.
Role of Maintenance:
- Proper Machine Setup & Alignment: Misalignment of punches and dies is a major cause of premature wear and catastrophic failure. Regular checks ensure precise alignment.
- Effective Lubrication: Consistent and correct application of high-quality cold forming lubricants is crucial. This reduces friction, prevents galling, and dissipates heat.
- Regular Inspection: Periodically inspecting dies for early signs of wear, hairline cracks, or material build-up allows for timely intervention.
- Planned Regrinding/Reconditioning: Dies can often be reground or resurfaced before failure becomes extensive. This extends their life significantly. Establish clear criteria for when to regrind.
- Proper Storage: Storing dies in a clean, dry, protected environment prevents corrosion, rust, and accidental damage when not in use.
- Monitoring & Data Analysis: Tracking die life and failure modes can provide valuable data. This informs future design improvements and material selections.
By integrating intelligent design with diligent maintenance practices, manufacturers can significantly enhance the reliability and performance of their cold forming operations.
Conclusion
Cold forming dies are vital for efficient fastener production, but their operational intensity makes them prone to specific failures like wear, cracking, chipping, and galling. Proactive prevention, rooted in a comprehensive understanding of these failure modes and their causes, is paramount. By rigorously applying best practices in material selection, precise heat treatment, intelligent die design, and consistent maintenance, manufacturers can significantly extend the lifespan of their dies. This approach not only reduces costly downtime and tool replacement but also ensures the consistent production of high-quality fasteners, cementing manufacturing efficiency and product reliability.
At Xiluo Mold, we recognize that preventing die failures begins at the design and manufacturing stage. With over 24 years of experience, we specialize in designing and manufacturing high-precision fastener molds and dies, engineered to resist common failure modes. As the only one-stop R&D and production screw mold factory in China, we meticulously control every step, from selecting high-quality imported steel and applying advanced heat treatment to ensuring optimized die design for durability. Our commitment to rigorous quality control helps us deliver tooling that maximizes uptime and produces consistent, high-quality fasteners for your most demanding cold forming operations.